Oil and Gas Industrial Filters
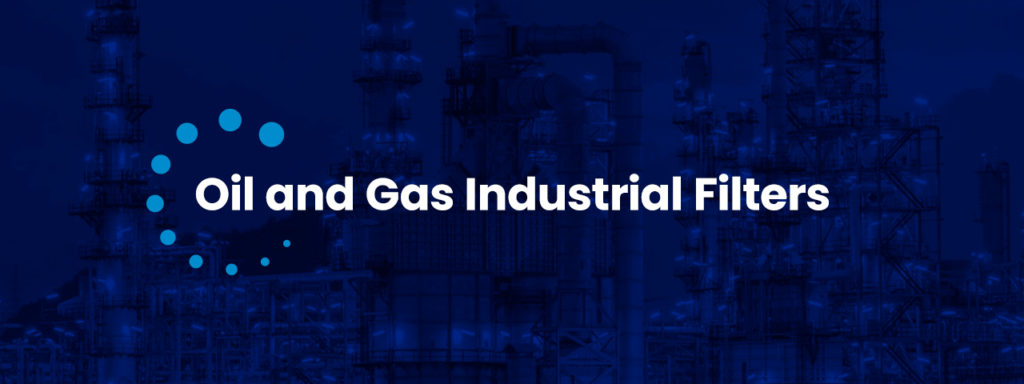
Many types of filters are useful in industrial applications. Filters help purify liquids and gases, removing contaminants. They help separate materials from each other, such as oil and water. They’re necessary for the smooth operation of machinery. Additionally, they promote safety and environmentalism — sophisticated filtration keeps waterways hazard-free and reduces air pollution.
Oil and Gas Filter Applications
Many different industries require the use of filtration systems. In the oil and gas industry, filters are a necessary component of everyday operations. Various types of filters serve many different purposes. Industry professionals use filters to separate, purify and recycle materials — including gas, water and oil. For any such application, filters are always necessary. A few of the oil and gas industries that use filters include:
- Fracking
- Off-shore production
- Steam flooding or steam driving
- Steam-assisted gravity drainage
- Disposal
- Onshore drilling
- Onshore transport
- Offshore transport
- Storage
- Refineries
- Petrochemical plants
- Natural gas (CNG)
- Sample analyzer equipment
- Drilling services
- Blenders
- Chemical vans
- Flair off trucks
- Frac pumpers
- Picker cranes
- Pumper trucks
- Sand kings
- Service rigs
- Shakers
- Top drive systems
- Vacuum trucks
- Water haulers
- Wireline trucks
- Workover rigs
All stages of the oil and gas industry require various filters for smooth, efficient and safe operation. The stages include upstream, midstream and downstream.
Upstream facilities have to manage waste products and maximize raw material recovery. Midstream facilities have to keep materials separate and uncontaminated during transportation. Downstream facilities have to create a safe, useful product for consumers. Learn more about each segment’s filtration needs.
Upstream Facilities: Exploration and Production
Upstream facilities are involved with the discovery, extraction and production of raw materials. They are the exploration and production segment of the oil and gas industry and are the first in the supply chain. Filters designed for material separation are vital to this step in the process. Using proper filtration increases oil recovery and output.
Additionally, filters are necessary for removing harmful contaminants for safe waste-material disposal. Upstream facilities have to meet certain standards to maintain the wellbeing of nearby communities and natural environments.
Heavy bromides and chlorides are the fluids that are typically used in oil-well completion. They contain dirt particles that can decrease the reservoir’s permeability and reduce productivity.
The pleated-filter, absolute-rated cartridges available from Chase Filters ensure all down-well fluids are free of particulate, which protects the well permeability and maintains the continuous flow of oil fluids. Applications include:
- Air compressors
- Analysis equipment
- Blenders
- Blow outer preventer actuation
- Chemical injection units
- Cooling fluids
- Downhole drilling tools
- Frac pumpers
- Hydraulic power units
- Hydraulic winches
- Picker cranes
- ROV hydraulics
- Sample equipment
- Sand kings
- Seawater injections
- Seismic systems
- Service rigs
- Subsea tie-back systems
- Top drive systems
- Water haulers
- Watermakers
- Workover
Midstream Facilities: Refining, Petrochemical and Storage
From the North Atlantic to South America to the Pacific Rim to the Middle East — you will find Chase Filters in the oil & gas marketplace. Midstream facilities are the transportation and storage element of oil and gas supply. They receive raw materials and relocate them to final-step downstream facilities. During the transportation process, filtration is an absolute must. Filters keep solid particulate from contaminating oil and gas. If filtration is neglected during the midstream phase, downstream facilities have to set aside time for costly corrections. Applications include:
- Air compressors
- Analysis equipment
- Cargo tank inerting
- Casing and cementing
- CNG compressor stations
- Coil tubing equipment
- Debutanizer column
- Electronic controls
- Fluid conditioning
- Instrumentation
- Measurement equipment
- Methane offloading
- Mobile drill rigs
- Mobile power generation
- Oil tankers
- Pipe handling equipment
- Pressure Reducing Skids
- Watermakers
- Well cleanout
- Well control
- Well stimulation
Downstream Facilities: Distribution and Wholesale
Downstream facilities provide the final steps in the oil and gas production process. They refine crude oil and process natural gas to make them suitable for consumer use. Both solid and fluid contaminants can affect the proper performance of refined oil and gas. To provide the best product for consumer use, filters are necessary for the downstream facilities of the oil and gas industry. Applications include:
- Analytical systems
- Bulk tanks
- Cooling water treatment
- Cracking unit
- Fluid analysis
- Fluid sample collection
- Fuel additive process
- Gas purification
- Gasoline line bleeding
- Liquid propane
- Pipeline pigging
- Pipeline purging
- Pipeline stripping
- Polymer manufacturer
- Process controls
- Sample conditioning
- Sour water stripper
- Sulfur recovery
- Tank reservoir
- Terminal
Chase Filters Oil and Gas Filters
Oil and gas applications require many different types of filters — pneumatic filters for compressed air and power tools, oxygen filters for safe breathing purposes and coalescing filters for removing water and vapor, as well as various strainers and valves. All stages of the oil and gas industry supply line require numerous filters.
Chase Filters offers a wide range of filters for all your oil and gas industry needs. Some of the filters you may require for oil and gas purposes include:
- Hydraulic and pneumatic filters: Hydraulic or pneumatic-powered machinery needs clean fluid to function properly. Contaminants can impair productivity and pose safety risks. High-pressure, stainless steel filters help keep your machinery free from contaminants.
- Oxygen filters: Access to uncontaminated oxygen is essential for those in the mining and oil industries. You need reliable high-pressure in-line oxygen filters to ensure safety.
- Coalescing filters: For compressed air and gas filtration, coalescing filters are necessary for removing water and moisture. When it comes to oil and gas purposes, efficient coalescing filters need to be able to withstand high temperatures and high pressures.
- Strainers or valves: You may also need strainers to ensure the removal of unwanted solids from your fluids and gases.
- Portable filtration units: Especially useful for midstream facilities, portable filtration units like drum toppers allow for effective filtration on the go.
- OXYCHECK valves: These are vital for promoting safety in high-pressure environments. Upstream facilities, gathering crude materials from underground, benefit from reliable OXYCHECK valves. They reduce the risk of fire and minimize fire destruction.
Custom Oil and Gas Filters
Sometimes standard filter models get the job done. Other times, you may need to invest in custom filters or filtration systems. If your machinery has nonstandard dimensions or measurements, mass-produced filters might not work. Older machinery may require components no longer on the market. In either case, you may need custom filters.
Even if standard filters fit well enough, you may be looking to streamline your operation’s efficiency with specialized filters. A sophisticated filtration system will improve your productivity ten-fold. Chase Filters will design and produce custom filters for you.
Custom-designed filtration will promote efficiency and decrease maintenance costs. When you design a custom filter with Chase Filters, we keep your specific renderings handy so you can reorder with ease. We can also create other custom components for any oil and gas industry machinery.
Oil and Gas Filter Benefits and Features
Proper filtration has many features and benefits. Filters are necessary for smooth operation as well as human safety. Consider these reasons for installing filters in your oil and gas applications:
- Filters clean fuel before it’s burned. This is an important safety feature of oil and gas filters. Burning contaminants can be extremely hazardous.
- Filters reduce foaming in amine contactors. Foaming renders amine filters much less useful. Using proper filters can help avoid this issue.
- Filters prevent plugging in water disposal wells. Water disposal wells are critical for safety purposes. Plugging hinders this process, so filtration to avoid plugging is vital.
- Filters reduce nozzle blockage in instrument controllers. For your instrument controllers to function, they need to be free from obstructions and blockages. Filters make this possible.
- Filters prolong machinery lifespans. Using proper filters puts less burden on all of your machinery, allowing your systems to last longer and minimizing your maintenance and repair costs.
Contact Chase Filters for Gas and Oil Filters
Proper filtration should always be a priority. It improves the efficiency of machinery, minimizes safety hazards and prolongs the lifespan of machinery. Filters help reduce foaming, prevent plugging and blockage and keep materials uncontaminated. For these reasons, filters are vital for all stages of the oil and gas industry.
Whether you’re looking for a complete, start-to-finish custom filtration design or simply a replacement filter for a piece of machinery, Chase Filters & Components can fulfill your filtration needs. To learn more about filter applications and benefits in the oil and gas industry, contact Chase Filters & Components today.
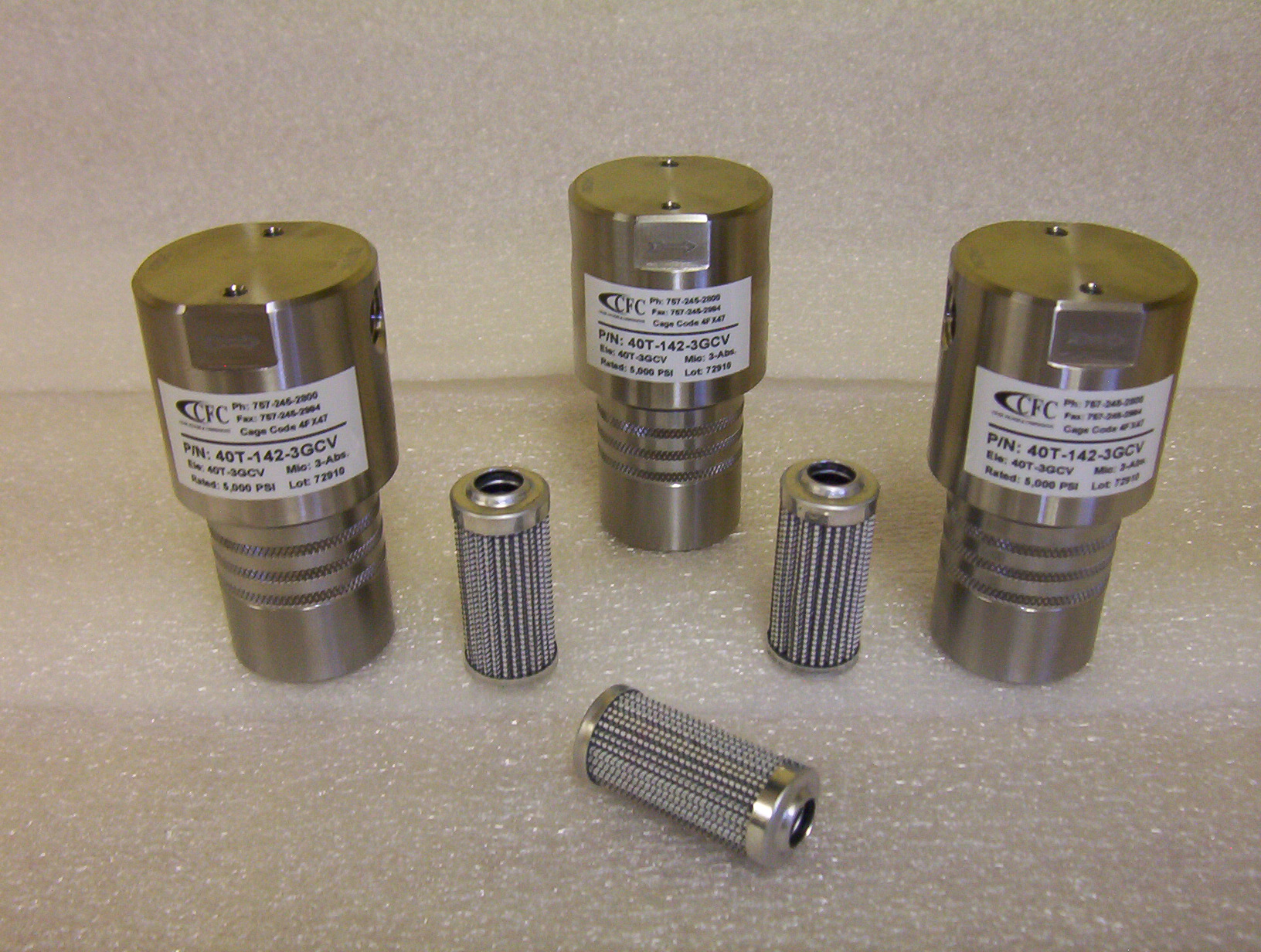